The energy crisis of the 1970s brought an end to the era of cheap oil and ushered in the race to drill for offshore oil. With the price of a barrel of crude oil in the double digits, some of the more sophisticated drilling and recovery techniques are beginning to be recognized, even if they are more expensive. By today's standards, early offshore platforms typically produced low volumes - around 10,000 barrels per day (BPD). We even have ThunderHorse PDQ, a drilling, production, and living module that can produce up to 250,000 barrels of oil and 200 million cubic feet (Mmcf) of gas per day. Such a large production unit, the number of manual valves as many as 12,000 more, most of them are ball valves. This article will focus on several kinds of cut-off valves commonly used in the upper facilities of offshore platforms.
Oil and gas production also requires the use of auxiliary equipment that does not directly perform the processing of hydrocarbons, but only provides relevant support for the process. Auxiliary equipment includes seawater lifting system (heat exchange, injection, fire fighting, etc.), hot water and cooling water distribution system. Whether it is the process itself or auxiliary equipment, it is necessary to use the partition valve. Their main functions are divided into two types: equipment isolation and process control (on-off). Below, we will analyze the situation of relevant valves around the delivery lines of various common fluids in offshore production platforms.
Equipment weight is also critical for offshore platforms. Every kilogram of equipment on the platform needs to be transported to the site across oceans and oceans, and it needs to be maintained throughout its life cycle. Accordingly, ball valves are most commonly used on the platform because they are compact and have more functions. Of course, there are more robust (flat gate valves) or lighter valves (such as butterfly valves), but considering various factors such as cost, weight, pressure and temperature, ball valves are often the most suitable choice.
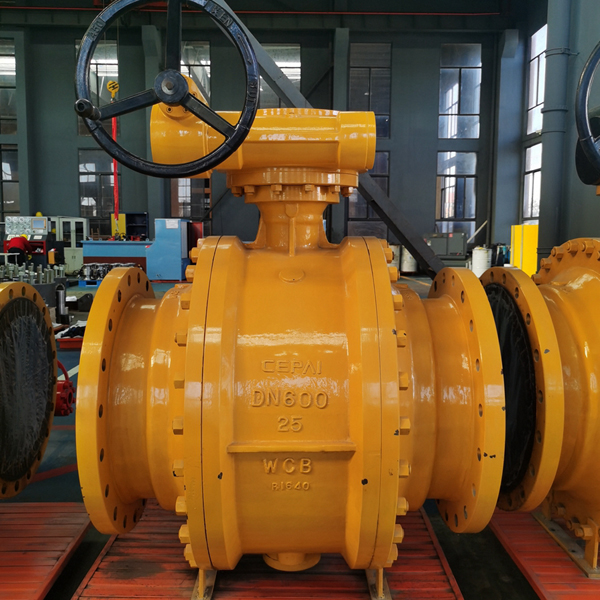
Obviously, ball valves are not only lighter, but also have smaller height dimensions (and often width dimensions). The ball valve also has the advantage of providing a discharge port between the two seats, so the presence of internal leaks can be checked. This advantage is useful for emergency shut-off valves (ESDV) because their sealing performance needs to be checked frequently.
The fluid from an oil well is usually a mixture of oil and gas, and sometimes water. Typically, as the life of a well ages, water is pumped up as a by-product of oil recovery. For such mixtures - and indeed for other types of fluids - the first thing to determine is whether there are any impurities in them, such as carbon dioxide, hydrogen sulfide, and solid particles (sand or corrosive debris, etc.). If solid particles are present, the seat and ball need to be coated with metal to avoid excessive wear in advance. Both CO2 (carbon dioxide) and H2S (hydrogen sulfide) cause corrosive environments, generally referred to as sweet corrosion and acid corrosion. Sweet corrosion generally causes uniform loss of the surface layer of the component. The consequences of acid corrosion are more dangerous, which often causes material embrittlement, resulting in equipment failure. Both types of corrosion can usually be inhibited by the selection of appropriate materials and the injection of relevant inhibitors. NACE has developed a set of standards specifically for acid corrosion: "MR0175 for the oil and gas industry, materials for use in sulfur-containing environments in oil and gas production." Valve materials generally follow this standard. To meet this standard, the material must meet several requirements, such as hardness, in order to be suitable for use in acidic environments.
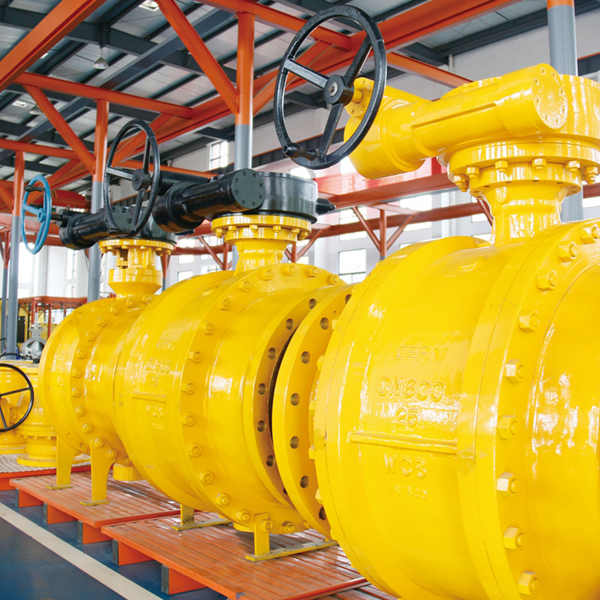
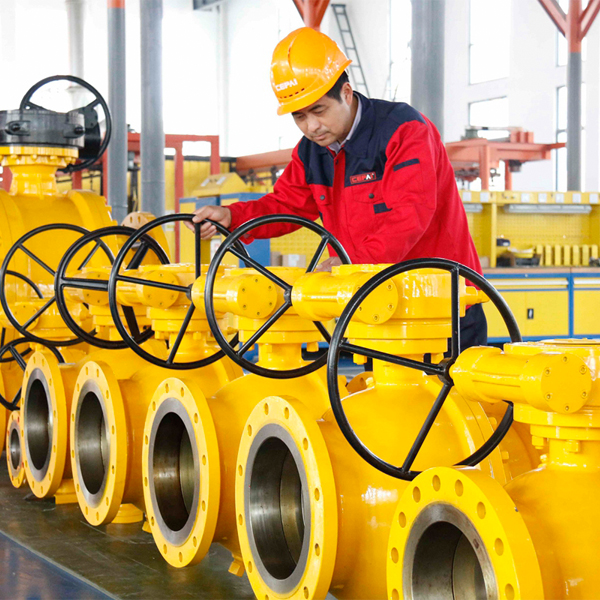
Most ball valves for offshore production are designed in accordance with API 6D standards. Oil and gas companies often impose additional requirements on top of this standard, usually by imposing additional conditions on materials or requiring more rigorous testing. For example, the S-562 standard introduced by the International Association of Oil and Gas Producers (IOGP). The S-562-API 6D Ball Valve Standard Supplement was developed by several major oil and gas companies to consolidate and streamline the various requirements that manufacturers must comply with. Optimistically, this will reduce costs and shorten lead times.
Seawater has a wide range of roles on drilling platforms, including firefighting, reservoir flooding, heat exchange, industrial water, and feedstock for drinking water. The pipeline transporting seawater is usually large in diameter and low in pressure - the butterfly valve is more suitable for the working condition. Butterfly valves comply with API 609 standards and can be divided into three types: concentric, double eccentric and triple eccentric. Because of the lower cost, concentric butterfly valves with lugs or clamp designs are the most common. The width size of such valves is very small, and when installed on the pipeline, it must be accurately aligned, otherwise it will affect the valve performance. If the alignment of the flange is not correct, it may hinder the operation of the valve, and may even make the valve unable to operate. Some conditions may require the use of double-eccentric or triple-eccentric butterfly valves; The cost of the valve itself is higher, but still lower than the cost of precise alignment during installation.
Post time: Jun-28-2024